Walkersele® Radial Lip Seals – General Range
Our family of high efficiency lip seals for rotary applications is extensively proven worldwide for long term bearing protection on plant as diverse as rolling mills, gearboxes, marine propulsion systems, process mixers, wind turbines, and tunnel boring machines.
Developed constantly over almost 60 years to keep ahead of customers’ operating conditions, Walkersele® offers many invaluable benefits to users.
- Highly cost effective
- Available in unlimited sizes
- Easy to install and simple to remove
- Supplied ex-stock in standard sizes
Walkersele® D1
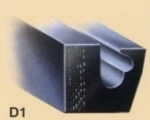
Original design modified for aggressive environments
- Exceedingly well-proven design of lip seal
- Modified Aflas® version now used on dewatering presses at pulp and paper plant
- Fabric-backed version available as Walkersele® OSJ-2 for On-Site Joining
Walkersele® D1/DL
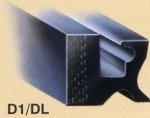
Alternative design with auxiliary dust-lip
- Similar to D6/DL – providing simultaneous fluid containment and dirt exclusion
- Alternative profile with dust lip incorporated in overall depth of seal
- Fabric-backed version available as Walkersele® OSJ-2 for On-Site Joining
Walkersele® D4

Slow rotary applications
- Moulded in elastomer-proofed fabric
- Developed for duties with highly abrasive media
- Used on pulverising mills, etc.
Walkersele® D5
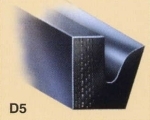
Compact design for limited housing space
- Very compact seal used where space is limited
- Feathered lip needs no spring for efficient operation
- Can be supplied with external lip for duties where sealing on inner periphery is impractical
Walkersele® D6
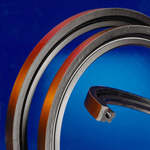
Our most popular design
- Minimal heat generation and shaft wear
- Flexible lip to accommodate shaft eccentricity
- Fabric-backed version can be supplied in split form and as Walkersele® OSJ-2 for On-Site Joining
- Standard inch and metric sizes ex-stock
Walkersele® D6/DL
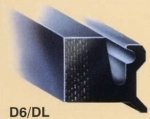
For aggressive environments
- Walkersele® D6 design with dust lip incorporatedfor simultaneous fluid containment and dirt exclusion
- Needs less space than double-seal arrangement
- Fabric-backed version available as Walkersele® OSJ-2 for On-Site Joining
Walkersele® D7
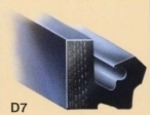
Pressure resistant lip seal
- Maximum operating pressure: 400 kPa without profiled lip support plate
- Flexible and robust lip maintains contact on shafts suffering slight eccentricity
- Available in self-retaining or plate-retained forms
- Fabric-backed version available as Walkersele® OSJ-2 for On-Site Joining
Walkersele® D8
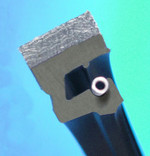
Developed for marine applications
- Also recommended for process equipment
- Accommodates shaft eccentricity
- Maximum service pressure: 150 kPa
- Withstands vibration and shock loads
- Fabric-back versions can be supplied in split form and as Walkersele® OSJ-2 for On-Site Joining
Walkersele® M1
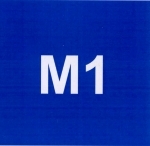
M1 – nitrile (NBR) elastomer
- Standard material for most Walkersele® applications
- Suitable for water and majority of oils and greases
- Construction: flexible back of NBR-proofed fabric, lip of NBR
Walkersele® M11
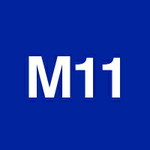
M11 – nitrile (NBR) elastomer
- For marine propulsion and power-train duties
- Suitable for duties submerged in salt water or fresh water
- Construction: back of nitrile-proofed aramid/glass fabric, lip of nitrile
Walkersele® M12
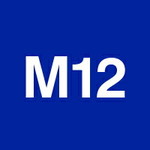
M12 – nitrile (NBR) elastomer
- For low temperature duties
- Usable range: -48 °C to +110 °C
- Construction: back of nitrile-proofed fabric, lip of nitrile rubber
Walkersele® M13
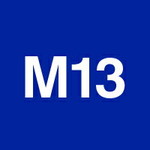
M13 – nitrile (NBR) elastomer
- Similar to Walkersele® M11, but for lower temperature duties
- Temperature range: -48 °C to +110 °C
- Construction: back of nitrile proofed aramid/glass fabric, lip of nitrile rubber
Walkersele® M22
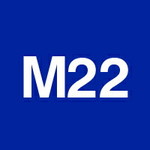
M22 – hydrogenated nitrile (HNBR) elastomer
- For wind turbine applications
- Long-term operation in harsh offshore and on-shore environments
- Temperature range: -25 °C to +150 °C
Walkersele® M5
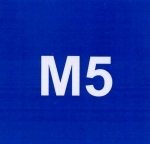
M5 – butyl (IIR) elastomer
- Often specified for its chemical compatibility
- Resistant to silicone oils and greases, acids, alkalis, salt solutions, alcohols, glycols
- Construction: flexible back of butyl-proofed fabric, lip of butyl
Walkersele® M6
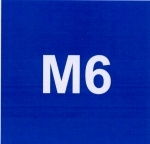
M6 – nitrile (NBR) elastomer
- Most popular material for self-retaining seals in open housings
- Suitable for use with most oils and greases
- Construction: nitrile NBR with stainless steel band encapsulated in its back
Walkersele® M8
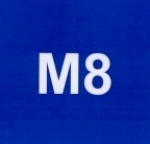
M8 – fluoroelastomer (FKM)
- High working temperature material for self-retaining seals in open housings
- Excellent resistance to lubricating oils, fuels, etc.
- Construction: fluoroelastomer with stainless steel band located in its back
Walkersele® M9
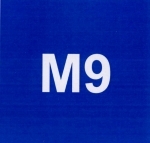
Walkersele® Millglide
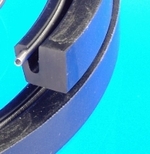
Reformulated HNBR material for Walkersele® on rolling mills
- Improved wear resistance over NBR
- Abrasion resistant material
- Superior high-temperature resistance than NBR
Walkersele® Supaglide
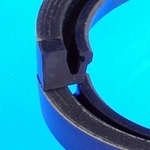
Reformulated HNBR for rotary seal duties at metallurgical plant
- HNBR formulated for running speeds up to 25 m/s
- Abrasion resistant
- For extended running life and reduced lifetime costs
Walkersele® Ultraglide

Reformulated HNBR elastomer for high temperatures and long life
- Highly extended sealing life with many fluid media
- Low friction material with greater abrasion resistance for improved running
- Improved heat dissipation for high efficiency sealing